Introducing Crown's Silent Rollers: Built Without Ball Bearings
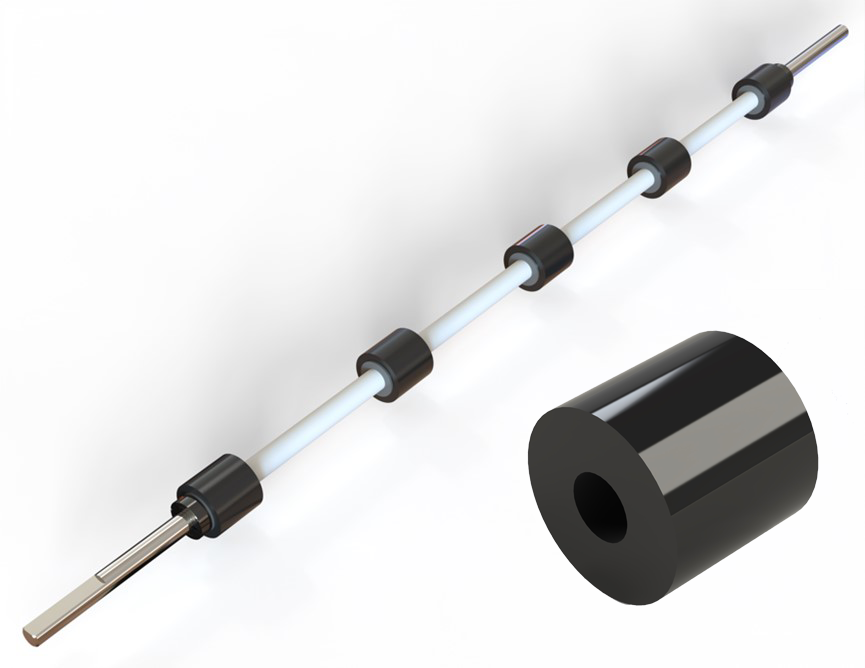
Crown's Silent Rollers are made with no ball bearings for quieter, more efficient operation.
Any way you look at it, distribution and material handling facilities are loud.
The rattle of conveyor belts. The forklift engines. The thrum of air compressors. While OSHA requires that workers not be subjected to noise over 85 dBA for a standard 8-hour shift, comfortable noise levels shouldn’t be any higher than 50 to 60 dBA. Levels higher than that will have a negative impact on worker safety and productivity. Excessive noise can even impact employee health, causing stress, hearing loss, tinnitus, and high blood pressure.
If you want a way to increase worker safety and productivity in distribution centers, you need to manage noise. Conveyor belts and conveyor belt rollers are major sources of excessive noise. A conveyor belt can exceed 95 dBA during peak operation.
Not only are conveyors loud, but they can lead to higher maintenance costs. A major conveyor problem is the ball bearings rattling around inside the metal rollers.
The Problem with Ball Bearing Rollers
In distribution centers, friction is the enemy.
Friction slows your packages, and a package with increased friction requires more time, effort, and cost to move from point A to point B.
Ball bearings reduce the friction in conveyor systems. They provide a steady, consistent platform for moving packages because they enable motion and reduce the surface area that creates friction. Motion on the belt or package is achieved not over a flat surface but on a rolling element (the ball bearing) that incorporates a smooth surface and (typically) a lubricant. This means less of the package weight is directly on the surface, and that surface moves more easily.
But all those little metal balls banging around in the roller cause noise. Conveyors are one of the most significant causes of excessive noise in distribution centers. The motion and movement of ball bearings in your rollers also cause maintenance issues — the banging around in rollers and constant friction can cause conveyor breakdowns.
Crown’s Silent Rollers: Reducing the Noise and Friction in Warehouses and Distribution Centers
Crown’s Silent Rollers eliminate ball bearings to directly address noise in distribution centers. Using Crown’s ultra-slick, high-quality UHMW instead of metal ball bearings means your conveyor systems run smoother with less friction and significantly less noise.
Silent rollers are safer than other options. No guard is required. They also reduce maintenance costs. Crown’s UHMW offers more wear resistance than stainless steel. Because the Silent Roller eliminates the ball bearings that contribute to the failure of your conveyor systems over time, you have a long-lasting solution for your distribution center. In fact, you may never need to buy a roller again.
With the Silent Roller, you have a safer, more comfortable work environment with much less noise. You need to replace your rollers less, saving money. You have the smooth, worry-free operation and reduced friction you need. You have lower maintenance costs, significantly less noise, and more comfortable and productive employees.
Learn More About Crown’s Silent Rollers and Products for Material Handling
Ready to transform your distribution center into a quieter, more efficient workspace? Contact Crown Plastics today to learn more about Silent Rollers and other innovative material handling solutions. Say goodbye to noisy, maintenance-intensive conveyor systems and hello to a smoother, more productive operation.